The Warabeya Nichiyo Group headquarters has installed monitors in every meeting room that enable meetings to proceed in a paperless manner, and is encouraging a shift from paper-based materials management to digital-based management.
● Conducting internal environmental audits
As part of our Eco Action 21 initiatives, Warabeya Nichiyo Foods Co., Ltd., conducts internal environmental audits at the headquarters and all of our plants to verify and correct problematic areas discovered on site, as well as documents related to laws and regulations. In addition to pointing out problematic areas, we also horizontally deploy positive aspects to each plant.
● Undertaking efforts to strengthen employee awareness
We post "conserve water," "save electricity," "sort trash," and other similar notices about the environment in an effort to encourage action among users and to strengthen awareness. In order to better the understanding among our foreign-national employees, we also put up notices in other languages besides Japanese as part of improvements intended to enable all employees to work together on this effort as one.
- 拡大
- Multilingual bulletin board (Tokyo Plant)
● Introducing LED lighting
By actively introducing energy-saving lighting fixtures, mainly LEDs, we are working to reduce the amount of heat generated by the fixtures themselves, and to reduce CO_{2} emissions. Warabeya Nichiyo Foods Co., Ltd., has already completed the conversion to LED lighting fixtures at 90% of our plants, and will soon replace lighting fixtures with LEDs at all of our plants.
● Going paperless
Like the headquarters, each Warabeya Nichiyo Foods Co., Ltd., plant is working under the theme of reducing copy paper use.
Our plants also use various forms for hygiene management, ingredient receiving and shipping, and production control, for example, so we are studying the possibility of switching control of these processes from a paper-based approach to a digital-based approach. We have already introduced these systems at some of our plants, and will verify their effectiveness before considering deployment to other locations.
Although we have taken steps to thoroughly prevent contamination from entering our plants, we are also studying this approach from the perspective of safety because going paperless is anticipated to be effective in preventing contamination caused by paper scraps.
● Implementing logistics initiatives
Several locations operated by Bestrans Co., Ltd., which handles our Logistics Business, have received Green Management Certification from the Foundation for Promoting Personal Mobility and Ecological Transportation.
The Green Management Certification System certifies transportation companies engaged in initiatives aimed at protecting the environment.
Having established an environmental policy and an environmental action plan, Bestrans Co., Ltd., is now working to introduce eco-drive and low-emission vehicles.
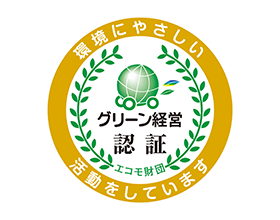